What is the production process of finned heat exchanger?
With the development of finned heat exchangers, it has become a mature heat exchange technology and become an indispensable general equipment in many industries. After innovative development, Guangzhou Lihe Haide's heat exchangers and heat exchanger units have produced plate heat exchangers with smaller footprint, higher heat exchange efficiency, and less scaling. Guangzhou Lihe Haide heat exchanger equipment can minimize the loss in the heat exchange process and maximize the utilization of heat energy, with high efficiency energy saving. Heat exchangers play an important role in various industrial and civilian fields, so what is the production process of plate heat exchangers? Lihe Haide will give you a simple explanation of the production process of plate heat exchangers so that you can better understand heat exchange equipment.
One, Design and Selection: Before producing and processing plate heat exchangers, we need to understand the type of heat exchanger that the customer needs, as well as the application field of the heat exchanger, in order to determine the model of the heat exchanger. More detailed selection parameters include specific cold and hot medium, inlet and outlet temperature, flow rate size, pressure requirements, interface size requirements, plate material requirements, gasket material requirements, etc. For selection issues, you can directly search for Guangzhou Lihei Heat Exchanger Equipment on Baidu and enter the official website for professional technical personnel to provide you with a full set of heat exchanger selection services.
Ⅱ.Selection of Materials After the customer selects the material and model of the panel, the production workshop will process the panel. The professional production panels are made with professional hydraulic machines, twice pressed into shape, and coated with soft processing technology. The panel forming precision is high and the quality is good. The wave depth of the panels is the same, ensuring the complete connection of all contact points between the panels.
Ⅲ.Assemble the plate heat exchanger. Clean all required parts first, then apply adhesive gasket sealant to the grooves; clean any residual glue from the grooves, and apply a synthetic resin adhesive to the plates before pressing the gasket into place. Then rotate the plates 180* in sequence, ensuring that no installation errors occur. When the plate bundle length reaches the calculated size, tighten the clamping bolts.
Ⅳ.Press forming. The formed panels, assembled with the bonding material, are pressed to ensure complete contact between the material and the bonding material.
Five, welding. According to the model of the plate heat exchanger required by the customer, weld the interface of different models together and weld the interface and its accessories onto the plate heat exchanger.
Six, leak detection and pressure testing: The specific method of leak detection for finned heat exchangers is to vacuum the heat exchanger and detect any leaks. Plate heat exchangers also need to undergo pressure testing at a pressure higher than the customer's requirements, usually nitrogen pressure, and then placed in a water tank for pressure testing to check for any leak points.
Ⅶ.Finished Product Drying, Packaging, and Transportation: After being subjected to rigorous testing, the qualified plate heat exchangers are dried to remove moisture and impurities, then packaged and transported.
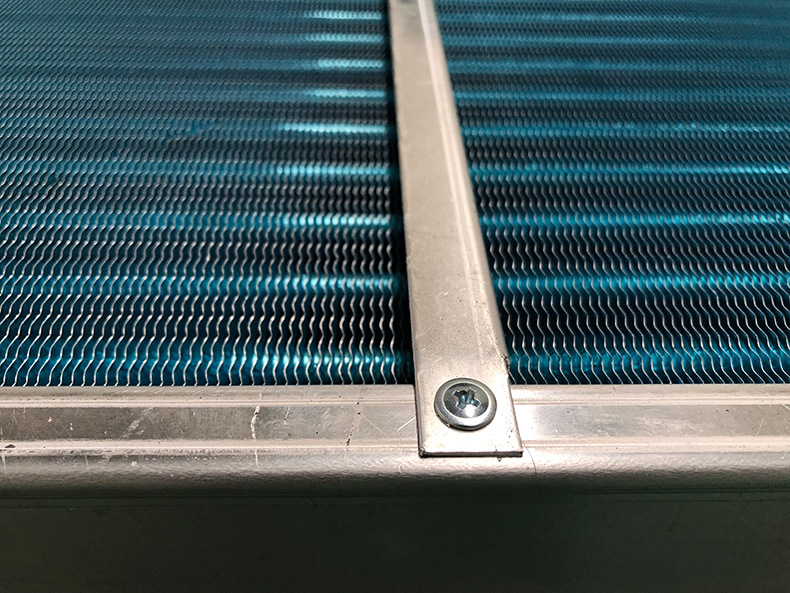